Innovation and Fabrication
Over the life span of a properly maintained aircraft many changes and improvements are likely to be needed and incorporated. The engineers and machine shop at JAARS do a wonderful job of designing and fabricating components when such a need arises. A good example of this process is their work redesigning the control stick of the PC-6 Pilatus, an aircraft used by JAARS for training and by YAJASI, our mission partner in Indonesia. The control stick is critical to the operation of an aircraft because it moves the flight control surfaces that cause the aircraft to climb, descend and turn.
The control stick actually required two modifications. The first stemmed from a request made by YAJASI to help them add an autopilot system to their fleet of four PC-6s. JAARS offered its Pilatus to be used as the test aircraft for this autopilot installation. A commercial avionics shop in Texas successfully installed the autopilot on our aircraft and added the controls onto the head of the control stick. Pilots soon discovered that this made the control stick taller, causing interference with a structural component in the cockpit when they moved the stick throughout its range. It was back to the engineering department at JAARS for a solution.

The solution was complicated by a previous modification JAARS had made. JAARS had installed an adjustable pilot seat on our PC-6 to enable shorter pilots to move the seat far enough forward to reach the rudder pedals comfortably. However, the PC-6 originally had a straight stick, and pilots had soon discovered that the seat interfered with full movement of the control stick with the seat moved forward.
With some skilled engineering and fabrication, JAARS workers had fabricated a curved control stick, which eliminated that problem. But now, that curved control stick had to be shortened to accommodate its larger head with the autopilot controls.
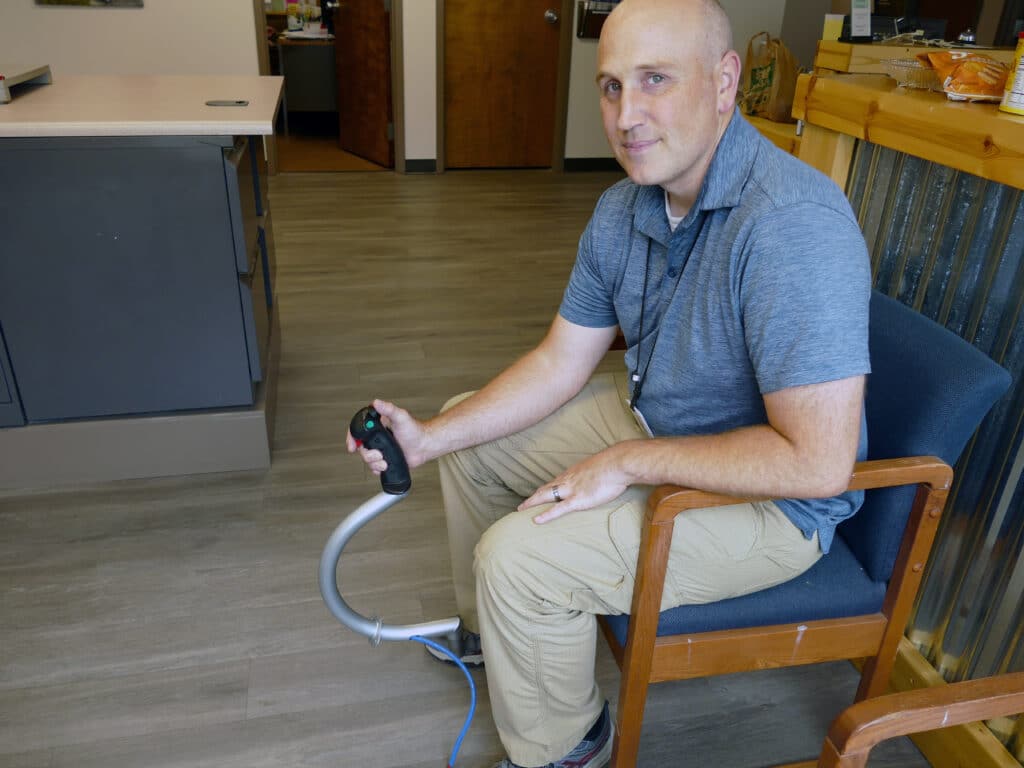
This was not an easy process. The new control stick had to be curved and welded precisely to ensure the delicate wiring running through the stick was not impinged or crimped. The bend in the control stick also had to be precise to ensure the correct height.

Fortunately, JAARS has the engineering and fabricating expertise to accomplish challenges such as this. One valuable tool in the process was a 3D printer JAARS has that could test a design and construct a model to check for accuracy before the fabrication process began. Terry Heffield, the engineer in charge of 3D printing, elaborated: “The 3D printers allow us to not only confirm that a design is the right shape, but it also confirms the sizes are correct. They are fantastic tools.”
Once the 3D model proved the design to be correct, the machine shop began the fabrication process. In the machine shop, Kyle Merkey and his crew made a bending die to form the curved stick precisely. Next they used a jig to securely hold the stick parts in place for the required precision welding. JAARS is blessed to have a highly skilled welder—Keith Wyckoff—who is a full-time volunteer at JAARS after retiring from a career in welding. Maintenance manager Matt Cousins described him as “’one of the most talented welders JAARS has ever had.” That expertise enabled him to get the welds exactly right where the bend in the control stick starts and stops.
JAARS mechanics will install the new control stick when our PC-6 comes into the hangar for scheduled maintenance this year. YAJASI will then have the option to install this improved design on their fleet of Porters when JAARS completes the required certification process, which is imminent. Once the new control stick is incorporated with the autopilot installation, pilots will find their workload reduced and flight safety increased as they face the demanding flying associated with mission aviation. This redesigned control stick is typical of the work JAARS does at its Waxhaw engineering and machine shop to resolve problems. They may operate “behind the scenes” but their products are way out front.